CEHIPAR
CEHIPAR provides a full set of services related to Numerical Hydrodynamics (CFD).
Projects of hull shapes and propellers, and their optimization before model tests in the towing tank, are done by means of numerical simulations or CFD (Computational Fluid Dynamics).
Flow around the hull for a velocity is optimized with CFD tools. Flow main characteristics as generated wave patterns, pressure and velocity fields, streamlines and resistance coefficients are obtained after computation.
Propellers are designed with specialized CFD software to calculate steady and unsteady forces, cavitation type, harmonics and pressure pulses in the stern.
Characteristics:
- Hull shapes:
Generalist CFD codes as ANSYS FLUENT, ANSYS CFX and OpenFOAM are the main tools used to study and modify hull shapes.
- Propellers:
Propellers’ performance is computed with the same generalist CFD codes used for hull shapes and some specific tools based on VLM lifting surface method. It is possible to compute sheet cavitation and wake alignment, adding viscosity, tip vortex and boundaries corrections. Hull-propeller interaction can be computed with low order panels and image methods.
Results:
The main numerical and graphical results are:
· Hull shapes:
- Pressure and velocity fields on hull surface and water free surface.
- Wave pattern.
- Wave profile.
- Limiting streamlines.
- Friction coefficient distribution.
- Boundary layer thickness.
- Lifting forces in lifting surfaces.
· Propellers:
- Main propeller curves and efficiency for different open water conditions.
- Thrust, power and propeller efficiency for a specific condition after the ship.
- Forces and torques pulses (6 components) on every blade and the shaft.
- Sheet cavitation performance in several blade positions
- Harmonics of the cavity volume change.
- Pressure distribution on the blades.
- Pressure pulses in the ship stern.
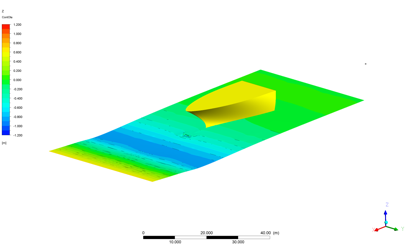